Daar is vandag drie tipes platglas in die wêreld: plattekening, dryfmetode en kalandering. Vloeiglas, wat tans meer as 90% van die totale glasproduksie uitmaak, is die basiese boumateriaal in die wêreld se argitektoniese glas. Die dryfglasproduksieproses is in 1952 gestig en het die wêreldstandaard vir hoëgehalte-glasproduksie gestel. Die dryfglasproses sluit vyf hoofstappe in:
● bestanddele
● smelt
● vorming en bedekking
● uitgloeiing
● sny en verpakking
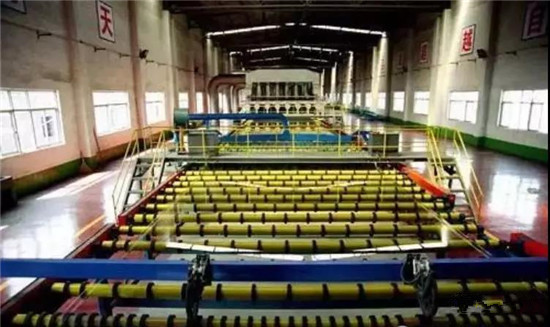
Bestanddele
Mengselvorming is die eerste fase, wat grondstowwe voorberei vir smelting. Grondstowwe sluit in sand, dolomiet, kalksteen, soda-as en mirabiliet, wat per vragmotor of trein vervoer word. Hierdie grondstowwe word in die mengselkamer gestoor. Daar is silo's, trechters, vervoerbande, geute, stofversamelaars en nodige beheerstelsels in die materiaalkamer, wat die vervoer van grondstowwe en die vermenging van mengselmateriaal beheer. Van die oomblik dat die grondstowwe by die materiaalkamer afgelewer word, beweeg hulle voortdurend.
Binne die mengkamer vervoer 'n lang plat vervoerband voortdurend grondstowwe vanaf die silo's van verskeie grondstowwe na die emmerhyser laag vir laag in volgorde, en stuur dit dan na die weegtoestel om hul saamgestelde gewig te kontroleer. Herwinde glasfragmente of produksielyn-terugvoere sal by hierdie bestanddele gevoeg word. Elke bondel bevat ongeveer 10-30% gebreekte glas. Die droë materiale word by die menger gevoeg en in die bondel gemeng. Die gemengde bondel word vanaf die mengkamer na die oondkopsilo gestuur vir berging deur die vervoerband, en dan teen 'n beheerde tempo deur die voerder by die oond gevoeg.

Tipiese Glassamestelling
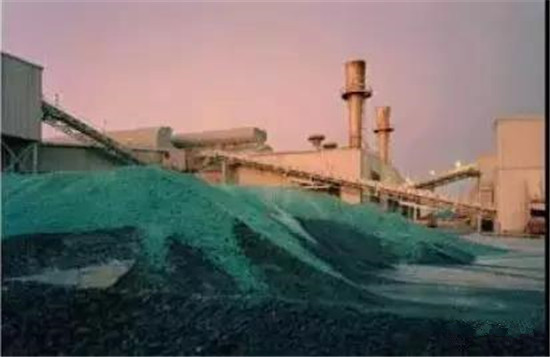
Cullet-werf
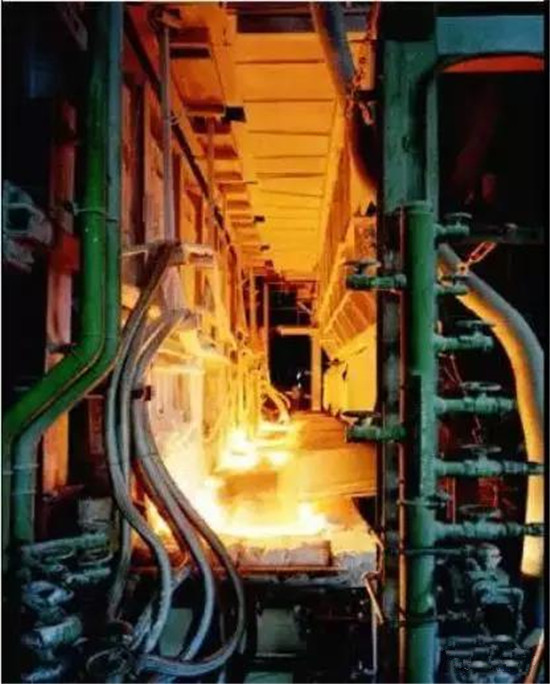
Voer die gemengde grondstowwe in die inlaat van die oond tot 1650 grade met 'n hopper
Smelt
'n Tipiese oond is 'n dwarsvlamoond met ses regenerators, ongeveer 25 meter breed en 62 meter breed, met 'n daaglikse produksiekapasiteit van 500 ton. Die hoofdele van die oond is die smeltpoel/verduideliker, werkpoel, regenerator en klein oond. Soos getoon in Figuur 4, is dit gemaak van spesiale vuurvaste materiale en het dit 'n staalstruktuur op die buitenste raam. Die bondel word deur die voerder na die smeltpoel van die oond gestuur, en die smeltpoel word deur die natuurlike gasspuitpistool tot 1650 ℃ verhit.
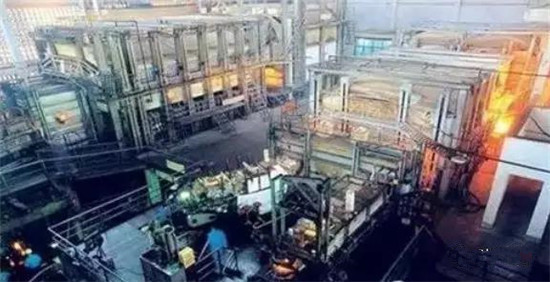
Die gesmelte glas vloei van die smeltpoel na die nekarea deur die suiweraar en word egalig geroer. Dan vloei dit in die werkende deel in en koel stadig af tot ongeveer 1100 grade om die korrekte viskositeit te bereik voordat dit die tinbad bereik.
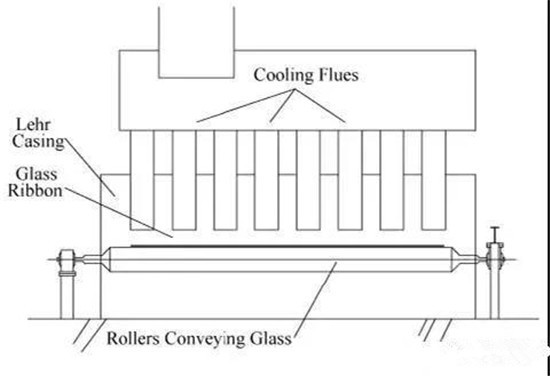
Vorming en bedekking
Die proses om die geklaarde vloeibare glas in 'n glasplaat te vorm, is 'n proses van meganiese manipulasie volgens die natuurlike neiging van die materiaal, en die natuurlike dikte van hierdie materiaal is 6.88 mm. Die vloeibare glas vloei uit die oond deur die kanaalarea, en die vloei daarvan word beheer deur 'n verstelbare deur genaamd die ram, wat ongeveer ± 0.15 mm diep in die vloeibare glas is. Dit dryf op gesmelte tin - vandaar die naam dryfglas. Glas en tin reageer nie met mekaar nie en kan geskei word; Hul wedersydse weerstand in molekulêre vorm maak die glas gladder.
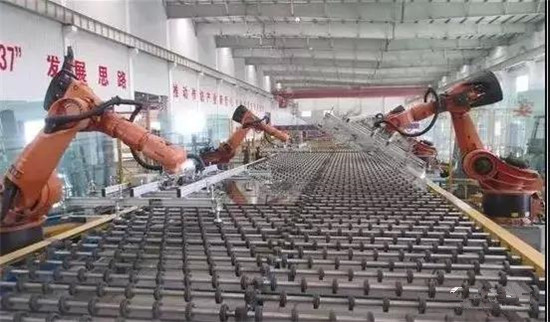
Die bad is 'n eenheid wat in 'n beheerde stikstof- en waterstofatmosfeer verseël is. Dit sluit ondersteunende staal, boonste en onderste doppe, vuurvaste materiale, tin- en verwarmingselemente, reduseer-atmosfeer, temperatuursensors, rekenaarprosesbeheerstelsel in, is ongeveer 8 meter breed en 60 meter lank, en die produksielynspoed kan 25 meter/minuut bereik. Die tinbad bevat byna 200 ton suiwer tin, met 'n gemiddelde temperatuur van 800 ℃. Wanneer die glas 'n dun lagie aan die einde van die tinbad-inlaat vorm, word dit die glasplaat genoem, en 'n reeks verstelbare randtrekkers werk aan beide kante. Die operateur gebruik die beheerprogram om die spoed van die gloeioond en randtrekmasjien in te stel. Die dikte van die glasplaat kan tussen 0.55 en 25 mm wees. Die boonste partisie-verwarmingselement word gebruik om die glastemperatuur te beheer. Soos die glasplaat voortdurend deur die tinbad vloei, sal die temperatuur van die glasplaat geleidelik daal, wat die glas plat en parallel maak. Op hierdie stadium kan acuracoat gebruik word ® Aanlyn platering van reflektiewe film, lae-e film, sonbeheerfilm, fotovoltaïese film en selfreinigende film op pirolise CVD-toerusting. Op hierdie tydstip is die glas gereed om af te koel.
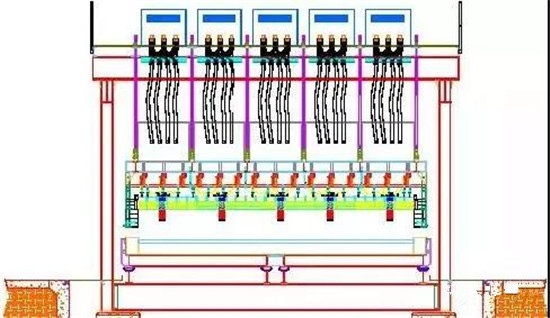
Bad Dwarssnit
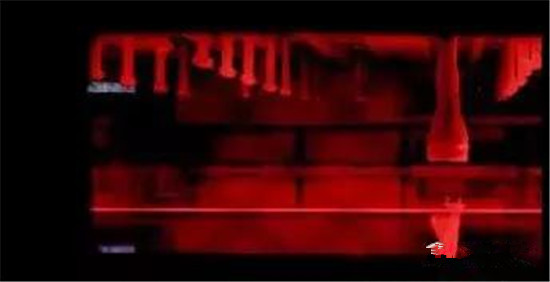
Die glas word in 'n dun lagie op die gesmelte blik versprei, apart van die blik gehou en in 'n plaat gevorm.
Die hangende verwarmingselement verskaf hittetoevoer, en die breedte en dikte van die glas word beheer deur die spoed en hoek van die randtrekker.
Uitgloeiing
Wanneer die gevormde glas die blikbad verlaat, is die temperatuur van die glas 600 ℃. As die glasplaat in die atmosfeer afgekoel word, sal die oppervlak van die glas vinniger afkoel as die binnekant van die glas, wat ernstige samedrukking van die oppervlak en skadelike interne spanning van die glasplaat sal veroorsaak.
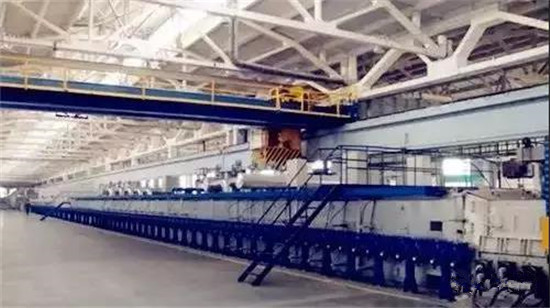
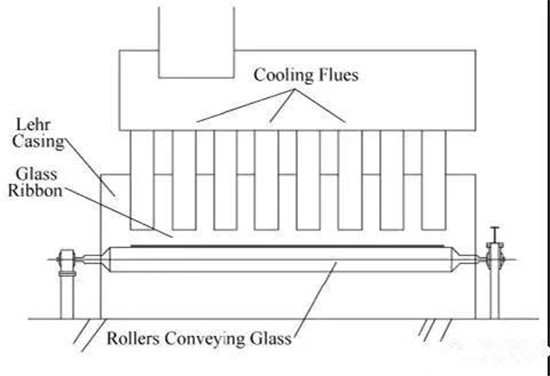
Afdeling van die uitgloei-oond
Die verhittingsproses van glas voor en na vorming is ook die proses van interne spanningsvorming. Daarom is dit nodig om die hitte te beheer om die glastemperatuur geleidelik tot die omgewingstemperatuur te verlaag, dit wil sê uitgloeiing. Trouens, uitgloeiing word uitgevoer in 'n voorafbepaalde temperatuurgradiënt-uitgloeioond (sien Figuur 7) van ongeveer 6 meter breed en 120 meter lank. Die uitgloeioond sluit elektries beheerde verwarmingselemente en waaiers in om die transversale temperatuurverspreiding van glasplate stabiel te hou.
Die resultaat van die gloeiproses is dat die glas versigtig afgekoel word tot kamertemperatuur sonder tydelike spanning of spanning.
Sny en Verpakking
Die glasplate wat deur die gloeioond afgekoel word, word deur die roltafel wat met die aandryfstelsel van die gloeioond gekoppel is, na die snyarea vervoer. Die glas slaag die aanlyn inspeksiestelsel om enige defekte uit te skakel en word met 'n diamantsnywiel gesny om die rand van die glas te verwyder (die randmateriaal word as gebreekte glas herwin). Dan word dit in die grootte gesny wat deur die kliënt vereis word. Die glasoppervlak word met poeiermedium besprinkel, sodat die glasplate gestapel en gestoor kan word om te verhoed dat dit aan mekaar vassit of krap. Dan word die foutlose glasplate in stapels verdeel vir verpakking deur hand- of outomatiese masjiene, en na die pakhuis oorgeplaas vir berging of versending aan kliënte.
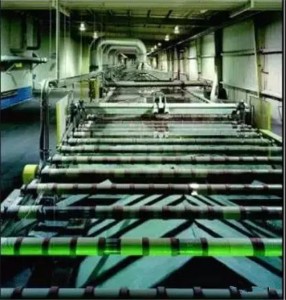
Nadat die glasplaat die gloeioond verlaat het, word die glasplaat volledig gevorm en na die verkoelingsarea verskuif om die temperatuur verder te verlaag.